    
Industrial Quad RC
Servo Motor Driver &
Potentiometers
Control Interface Board Module
is an Original Manufacturing Engineering (OEM) industrial and
commercial rated high performance, high efficiency
board that
utilizes potentiometers (POT) to control and drive both, RC
Servos, direction,
and angle.
The Quad RC
Servo Motors Driver & Control Interface Board Module power of
4 to 6VDC. An additional power input allows injection of higher
voltage to RC SERVO i.e. 7.4VDC, 12VDC etc.
The Quad RC-Servo Motor Driver & Control Interface Board Module
produces the required PWM multiplexing signals at 50 Hz of PWM
main frequency (period of 20ms) for controlling the RC Servo
motors. The PWM signal is used for controlling the motors
positions or directions. The positions and directions are direct
result of the potentiometers (POTs, Pots) positions. The driver
designed to support both, Industrial high quality RC Servo
motors that require 2000 levels corresponding to 0-5VDC POT’s
position and/or 255 levels standard of low quality RC Servo
motors.
Please be advised that the exact PWM width is depending on the
servo motor types and brands. Let our OEM engineer’s custom
“tailor” the Servo Motor Driver to meet your application
requirements and needs.
Two basic models are available - a built-in
potentiometers
and remote potentiometers (external
POT)
via wires and conveniently front mounted locking connectors.
The board also contains indication LED for Power
On (PWR ON) and Microcontroller Self Testing (MST). The LED will
blink "like HEART BEAT" once every second, indicating all of the
board functions are running and powered correctly.
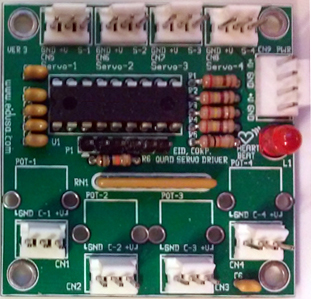
Shown above left, adjustments via
quad turn
potentiometers
(POT) and on the right control remotely via external
wired potentiometers.
The board offers the features
needed for professional setting Radio Control (RC) servo motors
position as a direct function of
potentiometer
movement.
Mounting is easy via four 0.156"
mounting holes using 6-32 screws and wire (optional) via
convenient conventional industrial standards locking connectors.
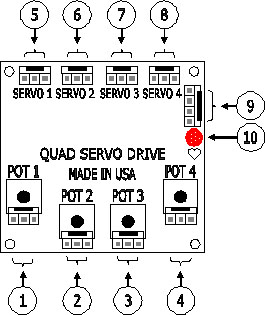
Quad RC
Servo Motor Driver & Control Interface Board Module basic
connections illustration
1.
First channel,
main on
board
potentiometer
(POT-1) model A or external of board via
locking type connector model B. Where; pins are marked (front left to
right) GND,
potentiometer
Center-tap (C-1), +V
2.
Second channel,
main on
board
potentiometer
(POT-2) model A or external of board via
locking type connector model B. Where; pins are marked (front left to
right) GND,
potentiometer
Center-tap (C-1), +V
3.
Third channel,
main on
board
potentiometer
(POT-3) model A or external of board via
locking type connector model B. Where; pins are marked (front left to
right) GND,
potentiometer
Center-tap (C-1), +V
4.
Forth channel,
main on
board
potentiometer
(POT-4) model A or external of board via
locking type connector model B. Where; pins are marked (front left to
right) GND,
potentiometer
Center-tap (C-1), +V
5.
First channel external RC-Servo locking type connector. Where; pins are
marked (front left to right) GND, +V, Signal (S-1)
6.
Second channel external RC-Servo locking type connector. Where; pins are
marked (front left to right) GND, +V, Signal (S-2)
7.
Second channel external RC-Servo locking type connector. Where; pins are
marked (front left to right) GND, +V, Signal (S-3)
8.
Second channel external RC-Servo locking type connector. Where; pins are
marked (front left to right) GND, +XV, Signal (S-4)
9.
External Power connections via locking type connector. Where; pins are
marked (front top to bottom) VX+, GND, +V, GND.
10. Heart-Beat LED indication.
In-circuit debugger/programmer:
The Quad RC Servo Driver board comes
(shipped) pre-loaded with software. Whoever, we can custom the
code/software (C or Assembler) to fit your OEM needs. It done easily via
Microchip's PICkit-2 or
PICkit-3 USB type Programmer/Debugger.
Shown above PIC-KIT-3 USB
programmer (optional) via dedicated on board 6 pins connector.
Connecting the PICkit3 to the RC Servo
Driver board through standard ICSP interface using 6-pin on board
connector. The programmer connector pin-out is shown in the figure
below:
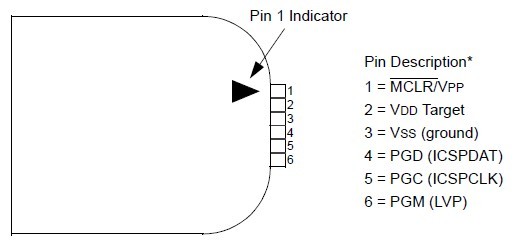
Please note the debugger
system can be configured to use standard
ICSP communication
for both programming and debugging functions. This PICkit-3
6-pin connection is the same one used by the older PICkit-2
Development Programmer/Debugger.
* The Microchip name and logo.
the Microchip, PIC, PICKIt 2, PICKIt 3 are register
trademark of Microchip Technology Inc.
Illustration:
RC Servo basic operation

Shown above
RC
Servo Motor basic operation illustration
Where;
T= 20.000mSec, t1= 1.000mSec, t2=
1.500mSec & t2= 2.000mSec, V = 4.8V to 24VDC (RC servo
motor depended) & 3 wires: Red = Power, Black = Ground & Yellow
= RC servo PWM signal.
Standard
Features:
● Provides motors with smooth
movement
●
Linear Adjustable via POTs
● High efficiency circuitry
● Conveniently front mounted
connections
● Conveniently front mounted LED
for both
power on and
Microcontroller Self Testing (MST) indicators.
Board
Dimensions:
Board width, length, height:
2.00" * 2.00" * 1.00"
Board
Mouthing Dimensions:
Four (4) mounting holes (.156"
Dia.) 1.70" * 1.70" on center.
Note:
Use four (4) 6-32 screws and stand-offs to mount the board.
Caution: Do not mount
the board where ambient temperature is outside the range of
-10° C (15° F) to 45° (115° F).
-20°C to +50°C (-4°F to 122°F).
Specifications:
Load current (continuous) |
< 80mA four RC servo motors |
Servo Motors Position adjustment |
Potentiometers 0 to +V (VDC) via 5K POT |
Acceleration |
0.1 seconds |
Deceleration |
0.1 seconds |
Angle |
Adjustable - -45 to 45 Degrees |
Connections |
POT and wires via locking connectors |
Operating temperature |
-20°C to +50°C (-4°F to 122°F) |
Board material |
FR4 |
Internal operating voltage |
About 12VDC model dependant |
Power Requirement |
4 to 6VDC and/or an additional 7.4VDC or
an additional 12VDC ±10% model
dependant at maximum of 3000mA (3A) |
|